Dans cet article, nous traiterons du concept mécanique du frein à disque, de son fonctionnement et de ses applications. L'article se terminera par un cas d'application.
A. Généralités sur les freins
Une définition simple du freinage est l'action d'imposer, à système mécanique en mouvement, une sollicitation visant à réduire sa vitesse ou à complètement en stopper le mouvement.
Il existent plusieurs types de systèmes de freinage. On peut les classer selon les actions mécaniques mises en jeu : freinage par friction, freinage électrique, freinage électromagnétique, freinage aérodynamique, ../
Dans la suite de cet article, nous allons intéresser à la catégorie de freinage par friction et plus particulièrement du système de frein à disque qui en fait partie.
Frein à disque : définition et principe de fonctionnement
Le frein à disque est un dispositif mécanique qui utilise la friction d'un élément du stator (les plaquettes) pour réduire la vitesse ou immobiliser l'élément en rotation, ici le disque, aussi appelé rotor.
Le frottement du stator sur le rotor génère de la chaleur dont la dissipation peut-être une problématique préoccupante suivant le type d'application.
Mettre une image d'un frein à disque
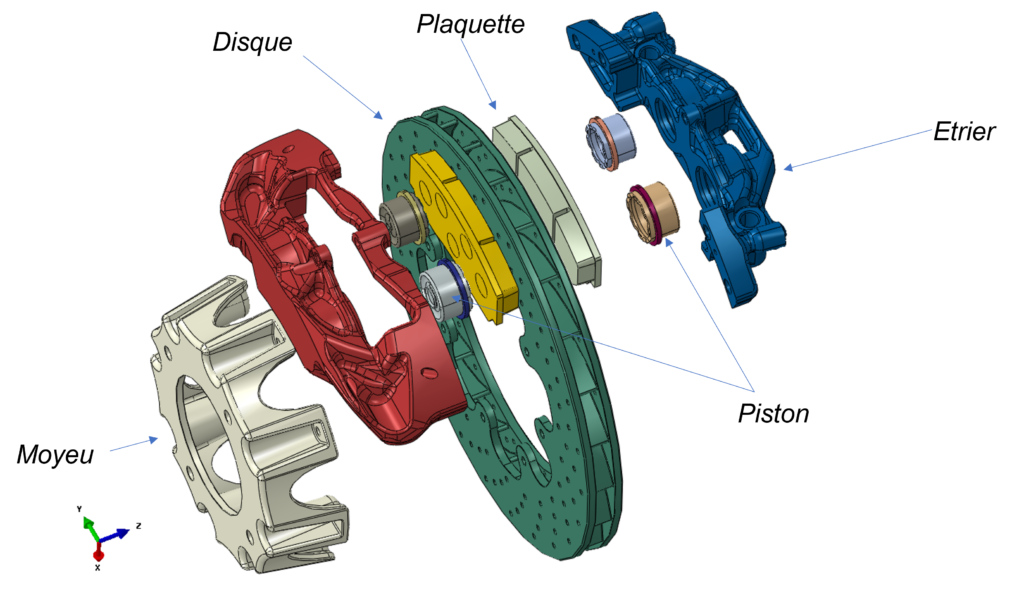
Exemple de système de frein à disque avec design ventilé
Applications des freins à disque dans l'industrie
Les freins à disques sont largement utilisés dans l'industrie du transport (ferroviaire, automobile, motocycle, aéronautique, vélo, véhicules lourds), dans les machines à commandes numériques, dans les machines tournantes, ...
Dimensionner un système de freinage
Le développement d'un système de freinage peut faire appel à plusieurs types d'analyse en fonction de la nature du produit et de la phase d'avancement de son développement. Le calcul par éléments finis est à ce stade vivement recommandé pour parvenir à une solution éprouvée et performante avec le minimum d'itérations de prototypes.
Voici quelques points à vérifier pour valider le dimensionnement :
1) La friction des plaquettes : Plus la friction est élevée, plus les plaquettes seront performantes. Avec les usages répétés, la surface active des plaquettes deviennent moins rugueuse (plaquette lisse), entrainant une perte de friction et donc une dégradation des performances de freinage.
2) La pression d'appui des plaquettes : Avec la friction, ce sont 2 paramètres qui agissent directement sur la performance du freinage. En situation exceptionnelle, lorsque l'un est défaillant, la surexploitation de l'autre peut dans une certaine mesure venir en compensation. Le dimensionnement de la pression exercée par les plaquettes est directement lié à celui de la commande de frein (actionneur pneumatique, hydraulique, électrique, mécanique,...) et aussi au design des plaquettes.
3) La dissipation de chaleur : Nous avons noté plus haut que le freinage par friction était générateur de chaleur. Dans certaines applications où les vitesses sont relativement et où les freinages peuvent êtres répétés à hautes fréquences, il est indispensable de s'assurer que système peut dissiper efficacement la chaleur, sans mettre le système en situation critique.
Dans ce cas, le design du disque doit être réalisé en tenant compte de cette problématique. Grâce à la simulation numérique couplés aux essais mécaniques, plusieurs concepts (disques rainurés, disques perforés,...) permettent aujourd'hui de ventiler efficacement les disques. En effet, avec le calcul par éléments finis, il est possible de modéliser les échanges thermiques de type conduction, radiation et convection avec la génération de chaleur.
4) La résistance structurelle : Le frein est un élément de sécurité. Par conséquent, sa tenue mécanique vis à vis de toutes les sollicitations évoquées plus haut doit être garantie. Dans ce contexte , la simulation numérique par éléments finis peut être un atout pour dimensionner le système de freinage avec une analyse couplée thermomécanique pour prendre en compte les contraintes et les déformations induites par la thermique et la mécanique.
5) L'analyse vibratoire : Pour aller un peu plus loin dans l'analyse, à haute vitesse, lors du freinage, la friction des plaquettes sur le rotor (disque) génère des points chauds qui déforment localement le rotor et modifient son comportement en rotation. Les vitesses critiques peuvent en être modifiées (voir article sur les rotors dynamiques).
6) L'analyse en fatigue : Le système de freinage est soumis à d'importants cycles de fonctionnement, à des intensités variables selon les applications. L'analyse en fatigue permet de déterminer la durée de vie de l'équipement. Elle peut être réalisée par essais et/ou simulation numérique.
Méthodes d'analyse numérique des freins à disques
Les méthodes et les outils de simulations numériques par éléments finis ont démontré leur capacité à résoudre avec une assez bonne fidélité les phénomènes physiques liés au freinage. Ces méthodes permettent des analyses individualisées des composants ainsi que des analyses globales du système mécanique concerné. Ils ont l'avantage d'offrir la possibilité de réaliser des plans d'expériences maîtrisés et des itérations beaucoup plus rapidement et ceux, en amont du prototypage réel. Idéalement, nous recommandons d'associer les deux méthodes pour que les modèles numériques soient validés par les essais.
Pour l'étude des systèmes de freinage, on peut réaliser :
- Analyse thermomécanique stationnaire ou transitoire : le choix entre la simulation stationnaire ou transitoire dépendra des applications, des vitesses en jeu et de l'objectif de l'étude.
- Une analyse vibratoire : voir article sur les rotors dynamiques
B. Exemple d'application
Nous allons étudier le temps de freinage d'un système de frein à disque de vélo de type VTT.
Les hypothèses de l'étude sont : une vitesse linéaire de 30 Km/h et une pression de plaquette sur le disque de 1 bar.
1) Description du système :
Nous allons étudier le temps de freinage d'un système de frein à disque de vélo de type VTT.
Les hypothèses de l'étude sont : une vitesse linéaire de 30 Km/h et une pression de plaquette sur le disque de 1 bar.
2) Propriétés mécaniques :
Le disque est conçu en acier et les plaquettes sont faites d'un matériau composite. Compte tenu de la vitesse de rotation relativement peu élevée, on fait l'hypothèse de propriétés mécaniques constantes en raison de la potentielle faible variation de température. Les propriétés matériaux sont résumées dans le tableau suivant :

3) Maillage :
Il se veut simple pour ce cas d'application. Des éléments volumiques de formes hexaédriques sont utilisés.
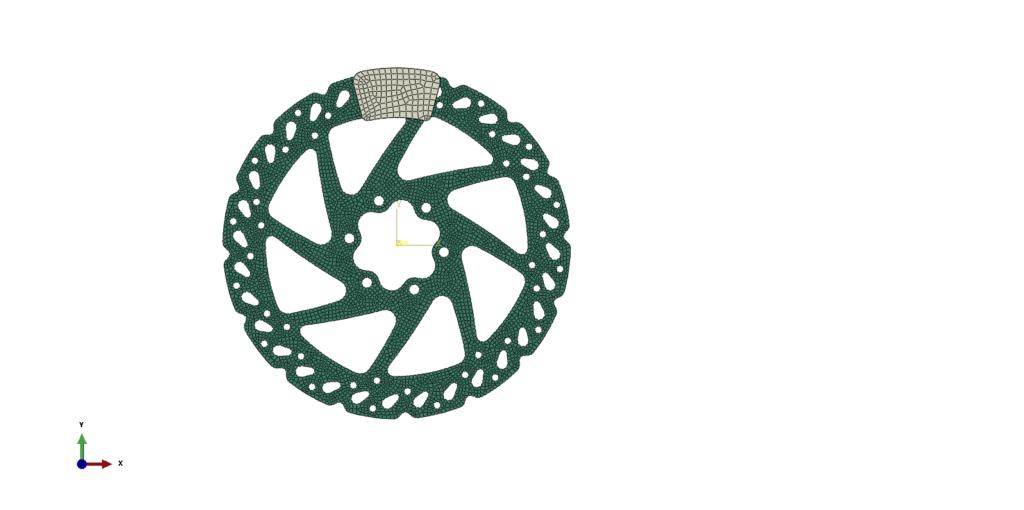
4) Approche de modélisation et étapes de calcul :
La modélisation par éléments finis se fera selon une approche directe couplée thermomécanique. Le solveur Abaqus Explicit sera utilisé. Le calcul comportera deux étapes. La première, durant laquelle le disque sera en rotation libre pour simuler la vitesse stationnaire atteinte par le cycliste. La deuxième sera celle du freinage.
5) Conditions limites :
La vitesse initiale de rotation du disque correspond à l'allure du vélo est appliquée. Les mouvements de l'axe du disque sont bloqués, seules sa rotation par rapport au même axe est autorisé.
Les mouvements de translations des plaquettes dans le plan de la surface du disque sont proscrits. Seule la translation direction normale au plan du disque est permise.
6) Cas de calculs :
4 cas de calculs sont réalisés. Les paramètres qui varieront sont la pression exercées par les plaquettes et le coefficient de friction.
Cas 1 : pression des plaquettes à 1 bar et coefficient de friction à 0.33
Cas 2 : pression des plaquettes à 1 bar et coefficient de friction augmenté de 10% (0.4)
Cas 3 : pression des plaquettes doublée (2 bars) et coefficient de friction à 0.33
Cas 4 : pression des plaquettes à 1 bar et coefficient de friction doublé (0.66)
7) Résultats :
La chaleur générée par le freinage est inférieure à 1°C. L'augmentation du coefficient de friction se traduit aussi par une augmentation de la chaleur générée.
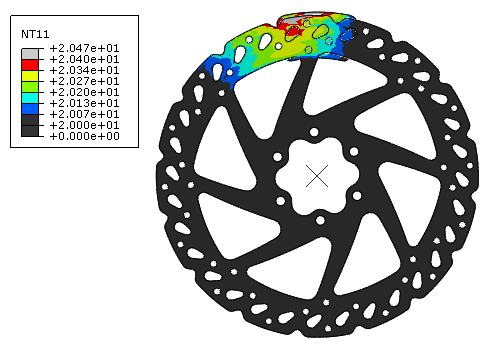
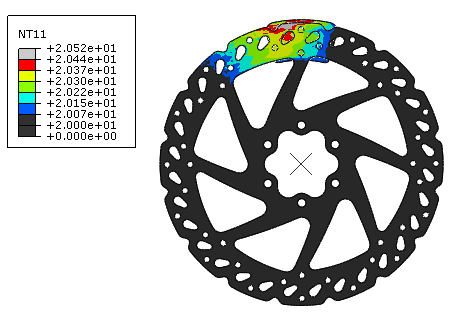
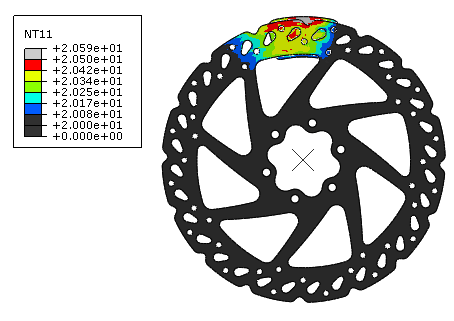
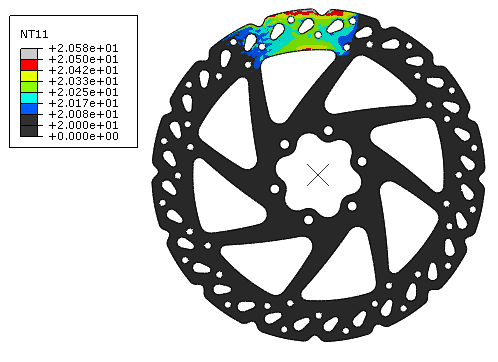
Les 4 cas de calcul ne permettent pas tous de totalement immobiliser la roue de vélo dans le temps imparti. Seuls les cas 3 et 4 parviennent à stopper complètement le mouvement du vélo.
La courbe de freinage met en évidence l'apport du coefficient de friction. Plus la friction est importante, plus le freinage est efficace.
Par ailleurs, l'augmentation de 100% de la pression exercée par les plaquettes produits les mêmes effets que la même augmentation du coefficient de frottement.
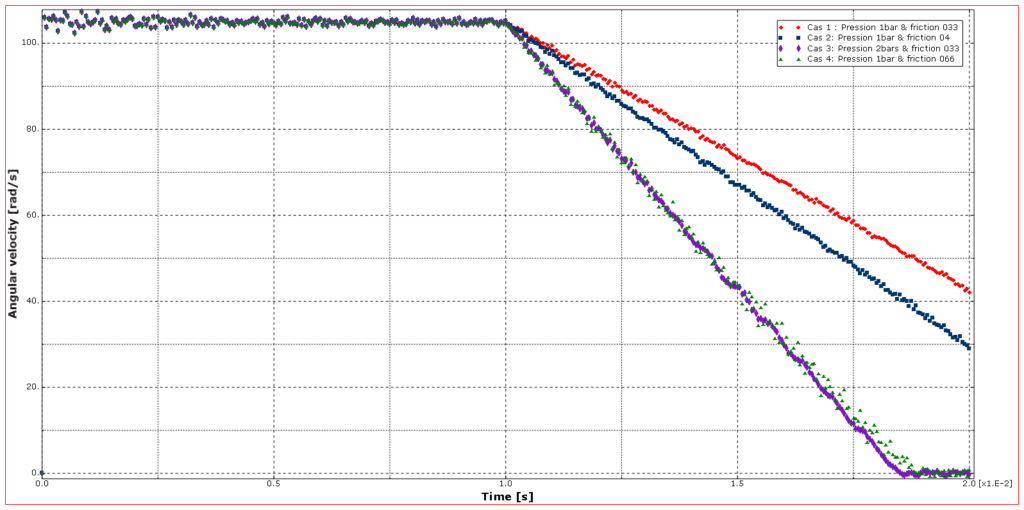
8) Conclusion :
L'augmentation du coefficient de friction est profitable aux performances du freinage mais génère aussi plus de chaleur. L'augmentation de la pression des plaquettes vient compléter l'action de la friction produites par les plaquettes. Si ces dernières sont défaillantes, l'exercice d'une pression plus importante peut compenser exceptionnellement pour obtenir des performances équivalentes.
Bibliographie
1. Emna SGHAIER. Dynamique des rotors à très hautes vitesses en régime non stationnaire – Identification par le filtre de Kalman. PhD thesis, Paris Saclay 2020
2. Sébastien ROQUES. Modélisation du comportement dynamique couplé rotor-stator d’une turbine en situation accidentelle. PhD thesis, Nantes 2007
3. Rim SINO. Comportement dynamique et stabilité des rotors: applications aux rotors composites. PhD thesis, Lyon 2007
Autres ressources
1. Jacques MAUREL. Unbalanced rotor behavior. Youtube channel
2. ONEPROD. Concepts of balancing: Types of Unbalance. Youtube channel
3. Grasp Engineering. Introduction to rotordynamic FE Analysis. Youtube channel
4. Rotor dynamics, Bearing, Motor. Rotor dynamics 101: Part 1 - Introduction. Youtube channel